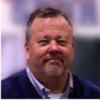
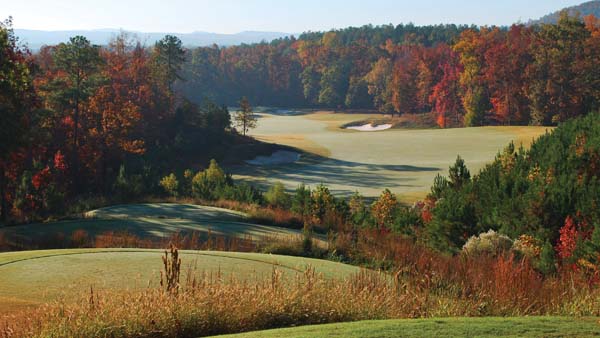
For the past 12 years, Langner was director of agronomy at Farm Links Golf Club in Sylacauga, Alabama. There he hosted more than 10,000 turf managers from throughout the country and around the world at Farm Links, which served as a research laboratory for testing a variety of turf management products and equipment. "Aqua-Aid has many moving parts, achieving tremendous growth over the past few years with our surfactants, Verde-Cal, and the Campey Imants line of equipment," said Sam Green, chief operating officer of Aqua-Aid. "Mark's unique background and his experience managing a variety of grasses in a research surrounding will be a huge benefit to our distributors and end users around the world for all aspects of our business. We look forward to Mark utilizing his knowledge and experience to continue to grow our portfolio." Aqua-Aid Inc. is the parent company for Aqua-Aid surfactants, Verde-Cal calcium and potassium products, and North American importer for the Campey Imants turf equipment.
- Read more...
- 2,861 views